- Crushing Screening Plants
- Sep 26, 2019
- 3 min read
Rock on Rock Vertical Shaft Impact Crusher MVI 90 started operation in the middle of the World for limestone crushing plant.
Meka MVI90 crusher has a tested and proven rotor that functions like a high-speed dry stone pump that launches rocks at a continuous pace.
The material fed into the machine accelerates in the rotor, and is continuously launched inside the crushing chamber at speeds of 50–75 m/sec. . This process forms a stone lining and causes the MVI90 to instigate a crushing and grinding chain reaction.
This, along with other variables, including rotor diameter, rotor speed and crushing chamber profile, can increase power efficiency, reduce abrasion, provide efficient control of the grinding and crushing process, and adjust the fineness of the produced material from minimum to maximum.
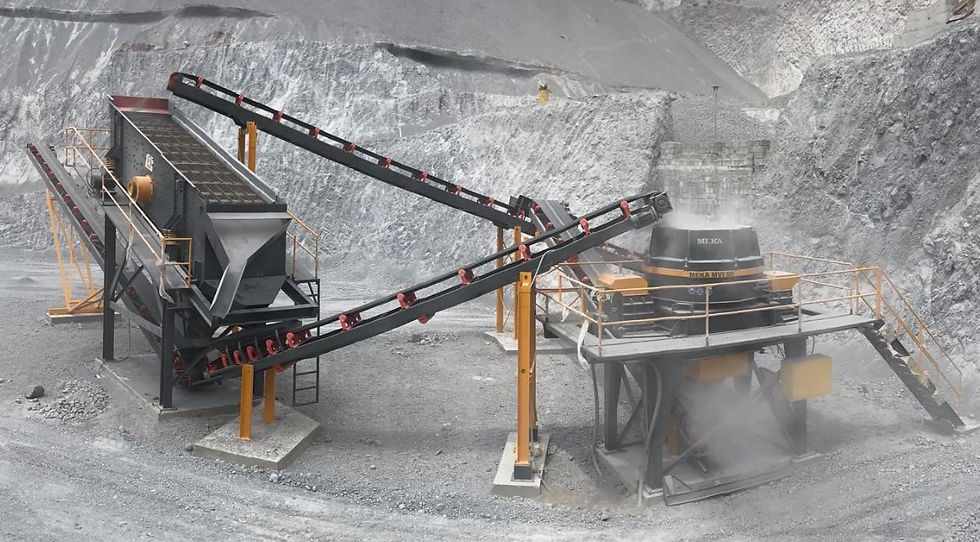
Vertical Shaft Impact (VSI) crushers are designed to be used in secondary, tertiary or quaternary stage crushing. The crushers are suitable for a wide range of applications including the production of high quality manufactured sand, well formed aggregates and industrial minerals. Crushers can also be used for shaping or removal of soft stone from aggregate. Advanced alternatives with open table designs, multi-port rotor and larger bearings than many other VSI crushers are the main reasons for our crushers to provide high value solutions and deliver high performance. We provide static, wheel mounted VSI plants and components. VSI Impact Crushers are suitable for manufactured sand, re-crush of slow selling stocks, cubical products fractured gravel, material beneficiation, crushing of cement clinker before mills and glass recycling applications.
Fully welded construction
Large receiving hopper
Heavy duty main pedestal
Drop in style, oil lubricated bearing assembly having ample dimensioned spherical roller bearings
Hydraulic lid lifter mechanism
Externally adjustable feed tube system with a convenient inspection door mounted on the lid, provides safe and easy inspection
Lid and main frame protection with special alloy wear resistant liners
Tungten carbide component on rotor
Preparations for water spray piping system mounting to avoid material build up underneath rotor V Belt drive guard prevents dust intrusion to the V Belt drive
Air transfer system enables internal air circulation and reduces dust emission
Bearing assembly mounted into a rigid base frame support provides maximum strength ideal for large feed or high speed applications
Flexible crushing chamber options
Modular oil system includes 160 liters(42 gallons) oil tank, gear pump, relief valves for low pressure oil circulation and high pressure lid lifter circuits, low flow rate shut down switch, oil heater, oil level gauge, oil temperature and lube oil pressure gauges
Safety features includes; open lid safety lock, low oil flow rate and high oil temperature shut off switches.
Excessive vibration alarm system that includes a maintenance alarm to alert you to potential problems. If excess vibration occurs, the vibration switch will shut down the crusher to protect it from possible damage.
Dual drive design reduces the radial and thrust loading on the electric motors, resulting in an extra-long service life for the motors
ROR configurations are recommended when crushing the most abrasive materials, in tertiary and quaternary applications where additional fines production is desired.
Autogenous crushing occurs inside crusher chamber between material thrown from rotor and material resting on rock shelf or material springing back from rock shelf.
Production of cubical high quality aggregates and sand from highly abrasive input materials, such as gravel, granite, quartzite etc
Crushing of highly abrasives materials, such as aluminum oxide, ferrosilicon, abrasives, glass etc
Selective crushing of slags from steel mills, waste incineration plants etc.